For more than 30 years, family-owned and operated CompressAir has served industries ranging from healthcare to construction with its impressive line of compressors and air treatment systems. The team that has been behind this success, CompressAir’s service department, regularly share their knowledge, expertise, and customer-first mindset to be the effective one-stop-shop it prides itself to be.
CompressAir’s service department provides preventive maintenance, 24/7 emergency maintenance, routine repairs, and installation of equipment and piping. The service departments in CompressAir’s Elkhart and La Porte locations have teams of skilled and knowledgeable parts managers, service coordinators and managers, and service technicians, ensuring that customers receive quality service through every step of the process.
“Combined, we have over 250 years of compressed air experience,” said Melisa Fisher, Parts Manager at CompressAir in Elkhart.Fisher handles the ordering and receiving of parts required to complete any job, a role that ensures service technicians are prepared in the field.
Dean Caldwell, Service Coordinator and Manager, has worked with CompressAir for more than 10 years. The expertise he has in compressed air systems and how they function, along with his desire to provide quality service to customers no matter their situation or needs, plays a vital role in making the service department’s maintenance plans and methods successful.
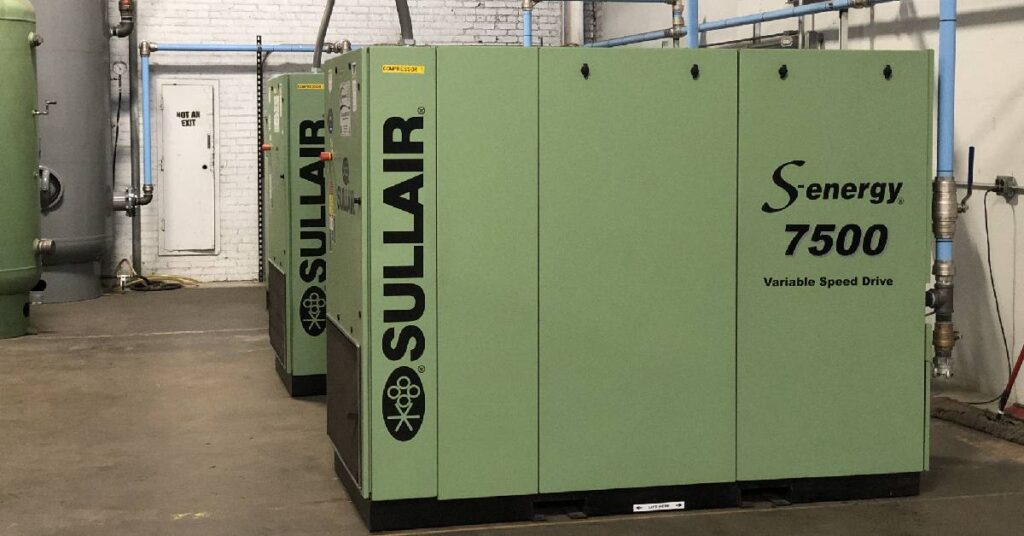
“Dean works with our customers to schedule preventive maintenance for equipment, schedules the technicians to jobs, and is a lifeline to our service technicians with questions they might have while out in the field,” Fisher said. “By having this process put into place on how things should run, we are able to all know what our tasks are, and we are able to successfully help out our customers.”
CompressAir’s service technicians are out in the community every day, performing preventive and emergency maintenance to customers in a variety of industries. No matter the type of repair, the skilled service technicians work hard to maintain the health of their client’s compressed air systems.
“Each of our service managers and technicians stays up to date on their Sullair Training and other major equipment competitors,” Fisher said.
They focus as much on education as in fixing problems.
“Our service department stresses that preventive maintenance helps equipment last longer,” Fisher said. “We want to be able to help our customers when an issue arises and before it is too late. By providing regular maintenance services, we are able to always keep tabs on how the equipment is running and are able to notice when there are major changes or issues to prevent more severe breakdown and downtimes in the future.”
“Keeping up with your preventive maintenance also helps to avoid emergencies. When emergencies happen and your equipment is down, that means you are also fighting the fact that you are unable to produce your product since air is needed in the production line,” she added.
Together, the CompressAir service department works to ensure that systems are working . For more information about CompressAir visit https://compressair.net/.